APQP
Advanced Product Quality Planning,
Teil der amerikanischen QS 9000 ist ein kontinuierliches Projektmanagement für die Produkt- und Qualitätsplanung und für alle Phasen des Entwicklungsprozesses geeignet.
Ziel ist, eine einheitliche produktbezogene Dokumentationsstruktur/-hierarchie zu haben, die dem Anwender (Hersteller) die notwendige Transparenz über das Herstellgeschehen liefern. Dadurch soll die Produktionslenkung vereinfacht werden. Alle projekt- und produktrelevanten Informationen und Dokumente werden zentral geplant, überwacht und verwaltet.
Teil der amerikanischen QS 9000 ist ein kontinuierliches Projektmanagement für die Produkt- und Qualitätsplanung und für alle Phasen des Entwicklungsprozesses geeignet.
Ziel ist, eine einheitliche produktbezogene Dokumentationsstruktur/-hierarchie zu haben, die dem Anwender (Hersteller) die notwendige Transparenz über das Herstellgeschehen liefern. Dadurch soll die Produktionslenkung vereinfacht werden. Alle projekt- und produktrelevanten Informationen und Dokumente werden zentral geplant, überwacht und verwaltet.
Validieren
Bestätigung durch Bereitstellung eines objektiven Nachweises, dass die Anforderungen für einen spezifischen beabsichtigten Gebrauch oder eine spezifische beabsichtigte Anwendung erfüllt worden sind. Die Anwendungsbedingungen für die Validierung können echt oder simuliert sein.
PPAP
Das Produktionsteil-Abnahmeverfahren (englisch: Production Part Approval Process (PPAP)) ist ein Verfahren aus der QS 9000, bei dem Serienteile bemustert werden.
Diese Vorgehensweise stammt aus der Automobilindustrie und wird dort seit Jahren erfolgreich umgesetzt. Dabei geht es vor allem um die Qualität der gelieferten Teile, das bedeutet, dass die Teile aus den Serienwerkzeugen bzw. Serienprozessen den Zeichnungen entsprechen müssen. Neben den zur Überprüfung gelieferten Teilen stellt die Bemusterung (englisch: part submission warrant (PSW)) ein zentrales Element für den Bemusterungsprozess dar. In ihm sind alle wichtigen Informationen zu Anforderungen und Tests zusammengefasst und dokumentiert.
Das genaue Vorgehen zum Beispiel bei der Bestellung der Teile und auch der Lieferung unterscheidet sich von Unternehmen zu Unternehmen durchaus sehr stark. Gleiches gilt auch für den Zeitpunkt der Bemusterung. So werden sicherheitskritische Teile schon lange vor Serienanlauf bemustert während andere Teile erst unmittelbar vor Produktionsstart zur Bemusterung gelangen. Allen Bemusterungen ist allerdings eines gemein: Die Einteilung nach 5 verschiedenen Ebenen der Bemusterung.
Diese Vorgehensweise stammt aus der Automobilindustrie und wird dort seit Jahren erfolgreich umgesetzt. Dabei geht es vor allem um die Qualität der gelieferten Teile, das bedeutet, dass die Teile aus den Serienwerkzeugen bzw. Serienprozessen den Zeichnungen entsprechen müssen. Neben den zur Überprüfung gelieferten Teilen stellt die Bemusterung (englisch: part submission warrant (PSW)) ein zentrales Element für den Bemusterungsprozess dar. In ihm sind alle wichtigen Informationen zu Anforderungen und Tests zusammengefasst und dokumentiert.
Das genaue Vorgehen zum Beispiel bei der Bestellung der Teile und auch der Lieferung unterscheidet sich von Unternehmen zu Unternehmen durchaus sehr stark. Gleiches gilt auch für den Zeitpunkt der Bemusterung. So werden sicherheitskritische Teile schon lange vor Serienanlauf bemustert während andere Teile erst unmittelbar vor Produktionsstart zur Bemusterung gelangen. Allen Bemusterungen ist allerdings eines gemein: Die Einteilung nach 5 verschiedenen Ebenen der Bemusterung.
PPAP, Forderungen
1. Designaufzeichnungen / Design Records
2. Dokumente über technische Änderungen / Engineering Change Documents
3. Technische Freigabe / Customer Engineering Approval
4. Konstruktions - Fehlermöglichkeits - und - Einflussanalyse / Design Failure Mode and Effects Analysis (D-FMEA)
5. Prozessflussdiagramme / Process Flow Diagrams (auch: Prozess-Ablauf-Plan PAP)
6. Prozess - Fehlermöglichkeits- und Einfluss Analyse / Process Failure Mode and Effects Analysis (P-FMEA)
7. Steuerungs- (Prüf-) plan / Control Plan
8. Analyse von Messsystemen / Measurement System Analysis Studies
9. Messergebnisse / Dimensional Results
10. Material- und Leistungstests / Records of Material / Performance Test Results
11. Untersuchungen zur Kurzzeitfähigkeit der Prozesse / Initial Process Studies
12. Dokumentation eines qualifizierten Laboratoriums / Qualified Laboratory Documentation
13. Bericht zur Freigabe des Aussehens / Appearance Approval Report
14. Muster - Serienteile / Sample Production Parts
15. Referenzmuster / Master Sample
16. Spezifische Prüfmittel / Checking Aids
17. Kundenspezifische Forderungen / Customer Specific Requirements
18. Teilevorlagebestätigung / Part Submission Warrant
2. Dokumente über technische Änderungen / Engineering Change Documents
3. Technische Freigabe / Customer Engineering Approval
4. Konstruktions - Fehlermöglichkeits - und - Einflussanalyse / Design Failure Mode and Effects Analysis (D-FMEA)
5. Prozessflussdiagramme / Process Flow Diagrams (auch: Prozess-Ablauf-Plan PAP)
6. Prozess - Fehlermöglichkeits- und Einfluss Analyse / Process Failure Mode and Effects Analysis (P-FMEA)
7. Steuerungs- (Prüf-) plan / Control Plan
8. Analyse von Messsystemen / Measurement System Analysis Studies
9. Messergebnisse / Dimensional Results
10. Material- und Leistungstests / Records of Material / Performance Test Results
11. Untersuchungen zur Kurzzeitfähigkeit der Prozesse / Initial Process Studies
12. Dokumentation eines qualifizierten Laboratoriums / Qualified Laboratory Documentation
13. Bericht zur Freigabe des Aussehens / Appearance Approval Report
14. Muster - Serienteile / Sample Production Parts
15. Referenzmuster / Master Sample
16. Spezifische Prüfmittel / Checking Aids
17. Kundenspezifische Forderungen / Customer Specific Requirements
18. Teilevorlagebestätigung / Part Submission Warrant
IATF
Die IATF (International Automotive Task Force) ist eine "zweckspezifische" Arbeitsgruppe, die sich aus Vertretern der (meist nordamerikanischen und europäischen) Automobilhersteller und Automobilverbänden zusammensetzt und sich mit der Harmonisierung (Vereinheitlichung) der Standards (Normen) zur Verbesserung der Produktqualität für Automobilkunden befasst.
CPK / CP
Der CpK-Wert wird folgendermaßen aus dem Mittelwert μ, der dazugehörigen Standardabweichung σ und der oberen (OSG) beziehungsweise unteren (USG) Spezifikationsgrenze definiert:

Je höher dieser Wert ist, umso sicherer befindet sich die gesamte Produktion innerhalb der Spezifikation.
Der Cp-Wert ist definiert als:
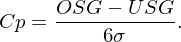
Der Cp-Wert lässt sich nur dann berechnen, wenn sowohl eine obere als auch untere Spezifikationsgrenze definiert ist.
Während der Cp-Wert nur das Verhältnis der vorgegebenen Toleranz zur Prozessstreuung angibt, beinhaltet der CpK-Wert auch die Lage des Mittelwertes zur vorgegeben Toleranzmitte. Daher ist der CpK-Wert stets kleiner als der Cp-Wert.

Je höher dieser Wert ist, umso sicherer befindet sich die gesamte Produktion innerhalb der Spezifikation.
Der Cp-Wert ist definiert als:
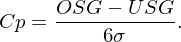
Der Cp-Wert lässt sich nur dann berechnen, wenn sowohl eine obere als auch untere Spezifikationsgrenze definiert ist.
Während der Cp-Wert nur das Verhältnis der vorgegebenen Toleranz zur Prozessstreuung angibt, beinhaltet der CpK-Wert auch die Lage des Mittelwertes zur vorgegeben Toleranzmitte. Daher ist der CpK-Wert stets kleiner als der Cp-Wert.
KVP
Kontinuierlicher Verbesserungsprozess oder kurz KVP (engl.: Continuous Improvement Process (CIP)) ist eine innere Haltung aller Beteiligten und bedeutet: stetige Verbesserung mit möglichst nachhaltiger Wirkung. Diese Haltung durchdringt dann alle Aktivitäten und das ganze Unternehmen. KVP bezieht sich auf die Produkt-, die Prozess- und die Servicequalität
Die 5 S-Bewegungen
Dabei handelt es sich um eine fünfstufige Vorgehensweise zur Neuplanung und Verbesserung von sauberen, sicheren und standardisierten Arbeitsplätzen.
* Seisō (Säubern: Den Arbeitsplatz sauber halten)
* Seiri (Sortieren: Ordnung schaffen, d.h. Trenne das Notwendige von dem nicht Notwendigen und entferne alles nicht Notwendige)
* Seiketsu (Standardisieren: zum Beispiel Reinigungspläne, Standard-Arbeitsplatz Layout)
* Shitsuke (Selbstdisziplin (engl. sustain): Erhaltung der Ordnung, Sauberkeit und Einhaltung der Standards)
* Seiton (Systematisieren: Jeden Gegenstand an dem richtigen Platz aufbewahren)
* Seisō (Säubern: Den Arbeitsplatz sauber halten)
* Seiri (Sortieren: Ordnung schaffen, d.h. Trenne das Notwendige von dem nicht Notwendigen und entferne alles nicht Notwendige)
* Seiketsu (Standardisieren: zum Beispiel Reinigungspläne, Standard-Arbeitsplatz Layout)
* Shitsuke (Selbstdisziplin (engl. sustain): Erhaltung der Ordnung, Sauberkeit und Einhaltung der Standards)
* Seiton (Systematisieren: Jeden Gegenstand an dem richtigen Platz aufbewahren)
Die 7 M-Checkliste
Hierbei handelt es sich um die 7 wichtigsten Faktoren, die immer wieder überprüft werden müssen:
* Mensch
* Maschine
* Material
* Methode
* Milieu / Mitwelt
Die ursprüngliche 5 M Methode wurde um zwei wichtige Faktoren
* Management und
* Messbarkeit
erweitert, da die Einflüsse des Managements im System und die Messbarkeit von einer bestimmten Tragweite sind.
* Mensch
* Maschine
* Material
* Methode
* Milieu / Mitwelt
Die ursprüngliche 5 M Methode wurde um zwei wichtige Faktoren
* Management und
* Messbarkeit
erweitert, da die Einflüsse des Managements im System und die Messbarkeit von einer bestimmten Tragweite sind.
Die 7 Verschwendungsarten
(Muda = japanisch für Verschwendung)
* Muda durch Überproduktion (mehr als notwendig fertigen.)
* Muda der Bestände (End-, Halbfertigprodukte, Zulieferteile u. Materialien die als Bestände lagern sind nicht wertschöpfend)
* Muda durch Nacharbeit/Fehler (Fehlerhafte Produkte stören den Produktionsfluss und erfordern teure Nachbesserung)
* Muda der Bewegung (Jede Körperbewegung, die nicht zum Wertzuwachs beiträgt ist unproduktiv)
* Muda in der Herstellung (Unzureichende Technologie oder Konstruktion)
* Muda durch Warten (untätige Hände eines Mitarbeiter. Prozesstaktung nicht optimiert)
* Muda beim Transport (Bewegung von Materialien oder Produkten ist nicht wertschöpfend)
Inzwischen werden oft 2 weitere Arten der Verschwendung diskutiert:
* Verschwendung durch schlechte Ergonomie (speziell im Hinblick auf Mitarbeiter)
* Nicht oder falsch genutztes Talent
* Muda durch Überproduktion (mehr als notwendig fertigen.)
* Muda der Bestände (End-, Halbfertigprodukte, Zulieferteile u. Materialien die als Bestände lagern sind nicht wertschöpfend)
* Muda durch Nacharbeit/Fehler (Fehlerhafte Produkte stören den Produktionsfluss und erfordern teure Nachbesserung)
* Muda der Bewegung (Jede Körperbewegung, die nicht zum Wertzuwachs beiträgt ist unproduktiv)
* Muda in der Herstellung (Unzureichende Technologie oder Konstruktion)
* Muda durch Warten (untätige Hände eines Mitarbeiter. Prozesstaktung nicht optimiert)
* Muda beim Transport (Bewegung von Materialien oder Produkten ist nicht wertschöpfend)
Inzwischen werden oft 2 weitere Arten der Verschwendung diskutiert:
* Verschwendung durch schlechte Ergonomie (speziell im Hinblick auf Mitarbeiter)
* Nicht oder falsch genutztes Talent
Poka Yoke
Der japanische Ausdruck Poka Yoke (jap. ポカヨケ, dt. „unglückliche Fehler vermeiden“) bezeichnet ein aus mehreren Elementen bestehendes Prinzip, welches technische Vorkehrungen bzw. Einrichtungen zur sofortigen Fehleraufdeckung und -verhinderung umfasst. Als Erfinder des Prinzips gilt Shigeo Shingo.
FMEA
Die FMEA (Fehlermöglichkeits- und Einfluss-Analyse) ist eine strukturierte, systematische Arbeitstechnik, um Fehlerrisiken bereits im Produktentwicklungsprozess zu identifizieren.
Ziel ist durch die Planung und Umsetzung geeigneter Maßnahmen Fehlerursachen und damit Fehler zu vermeiden beziehungsweise die Weiterleitung fehlerhafter Teile zu verhindern, wenn die Ursachenbeseitigung deutlich unwirtschaftlicher ist.
Ziel ist durch die Planung und Umsetzung geeigneter Maßnahmen Fehlerursachen und damit Fehler zu vermeiden beziehungsweise die Weiterleitung fehlerhafter Teile zu verhindern, wenn die Ursachenbeseitigung deutlich unwirtschaftlicher ist.
Tags: QM, QS, Qualitätsmanagement, Qualitätssicherung
Source: Wikipedia
Source: Wikipedia

Flashcard set info:
Author: touring-treiber
Main topic: Management
Topic: Qualitätsmanagement
School / Univ.: Quelle Wikipedia
Published: 18.09.2010